Entrevistas
Cómo un fabricante suizo de gafas utiliza la impresión 3D SLS para producir gafas de alta calidad
05 Julio 2022
Fabricación
Entrevista
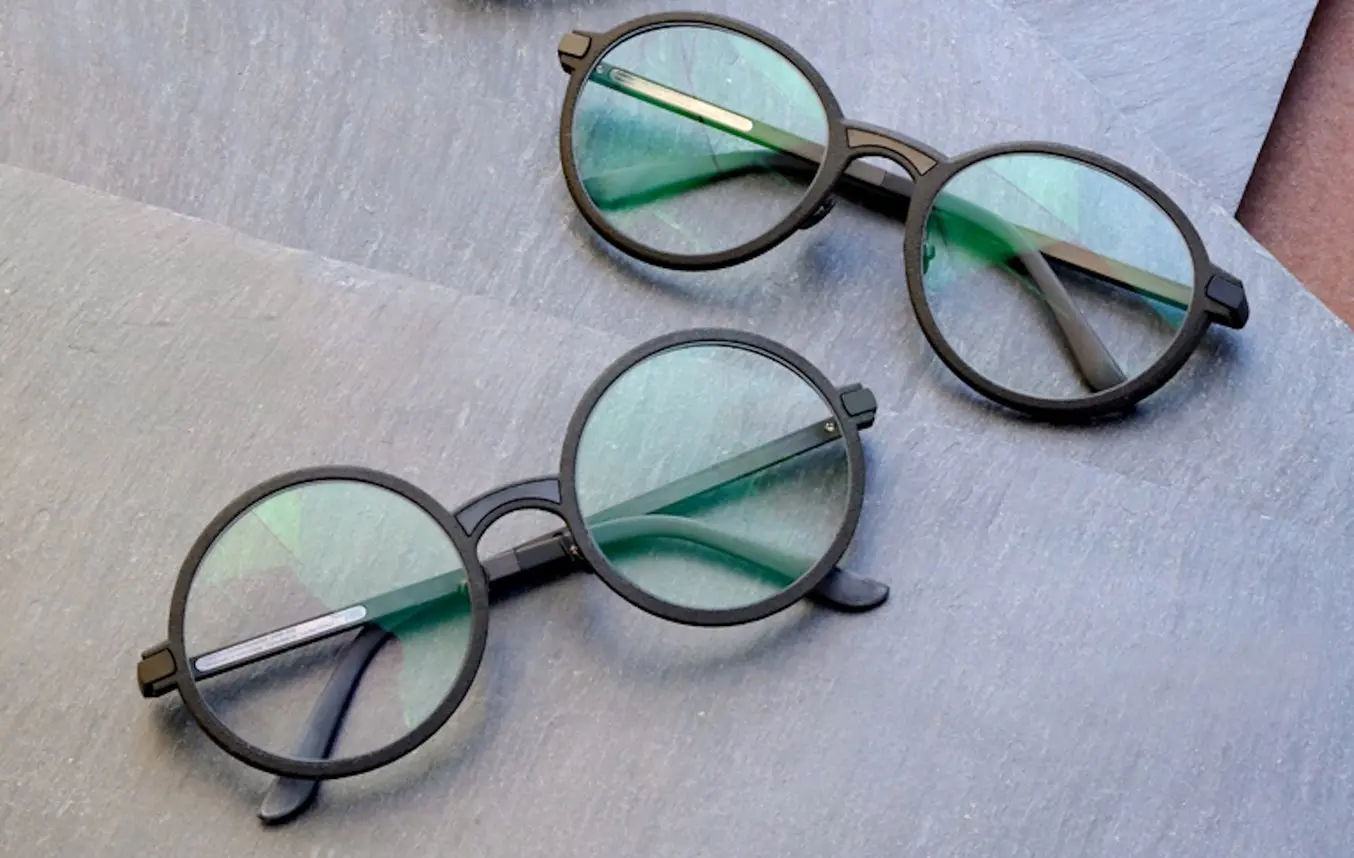
Gracias a su alta calidad, a la extravagante elección de los materiales y a su meticuloso trabajo artesanal, junto con ideas constantemente nuevas e innovadoras, las gafas de Marcus Marienfeld AG se distinguen claramente de las monturas de cristal convencionales.
Desde sus años de orfebre, Marcus Marienfeld siempre ha buscado la innovación y el desafío a la hora de diseñar y fabricar nuevos accesorios.
Recientemente, con una Fuse 1, integró la impresión 3D por sinterización selectiva de láser (SLS) en la línea de producción de sus monturas de cristal en su taller suizo para imprimir piezas de uso final y el utillaje rápido para el conformado de titanio.
En esta entrevista, nos habla de sus primeros pasos con la impresión 3D SLS, de las ventajas que le aporta tanto en la producción en serie como en los productos a medida, y de por qué le gusta tanto utilizar el nailon como materia prima.
De orfebre a fabricante de gafas
Marcus Marienfeld llegó a su actual hogar, Suiza, como orfebre. Rápidamente, vio el potencial de su sector para cambiar -incluso revolucionar- las técnicas de producción convencionales y, en su mayoría, obsoletas.
Su misión no era solo introducir la tecnología en el diseño de joyas, sino también en su producción.
Empezó con una empresa que desarrollaba colecciones de joyas y siempre se esforzó por llevar cada pieza del proceso a la empresa y fabricar el producto a mano, desde el dibujo hasta la construcción del modelo, pasando por la ejecución y la producción.
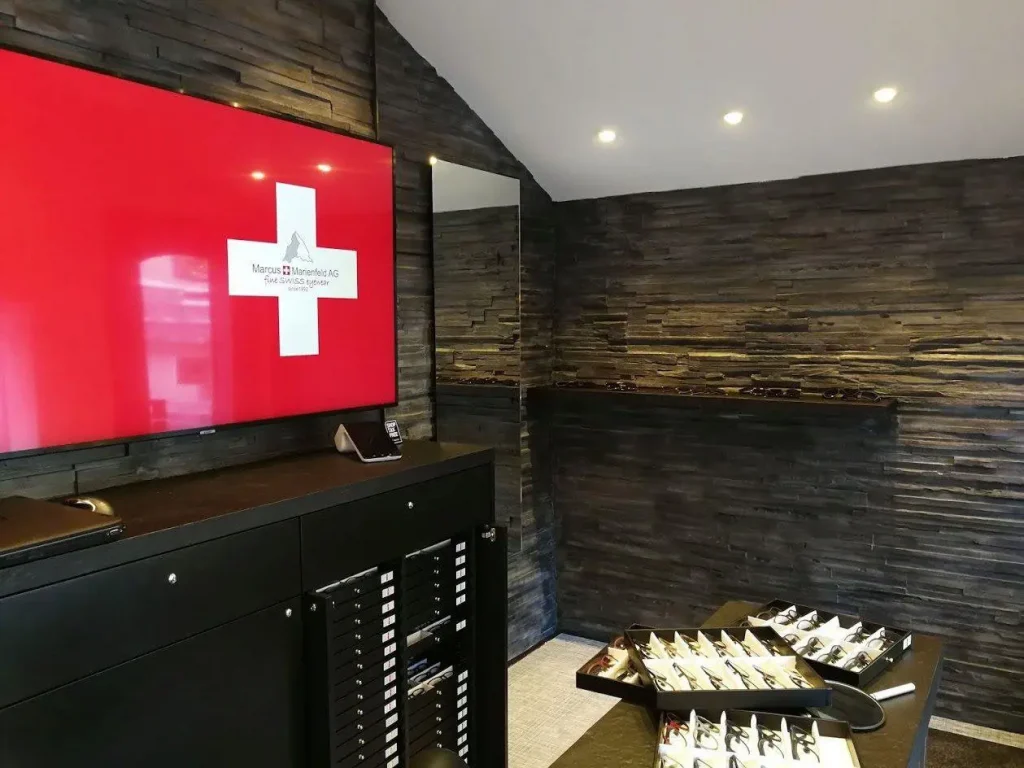
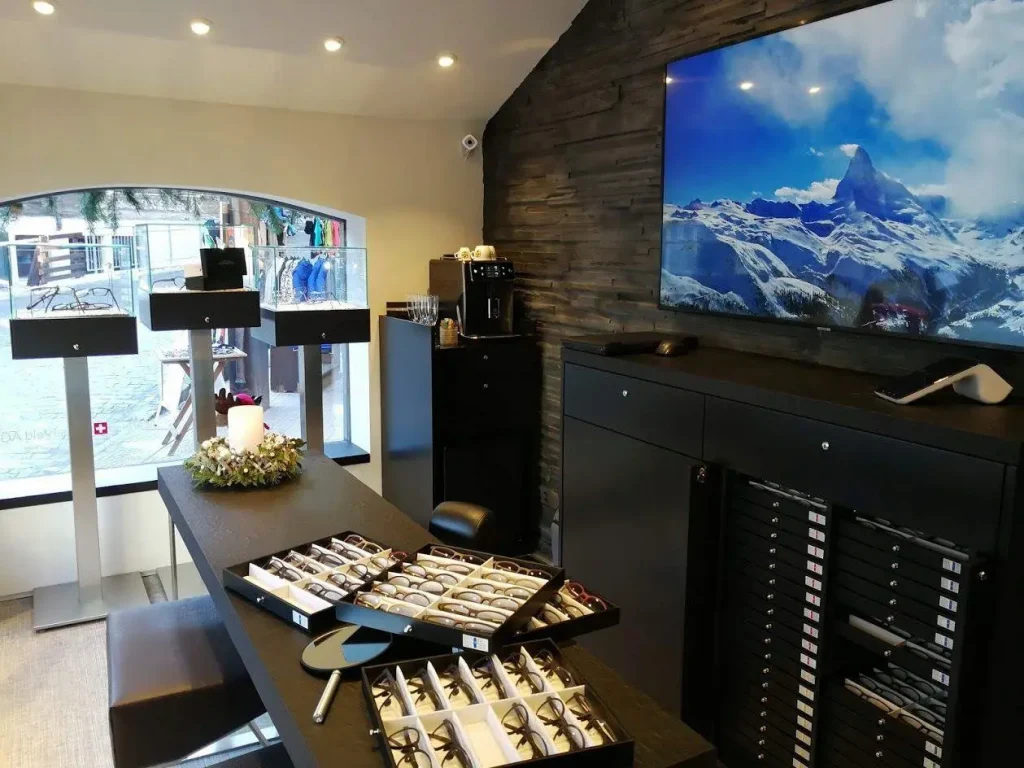
Como orfebre, primero utilizó la impresión 3D SLA para la creación rápida de prototipos de joyas y accesorios, antes de programar los diseños en una máquina CNC.
En la actualidad, Marienfeld emplea principalmente la impresión 3D SLS en su área de especialización: la fabricación de gafas. Su empresa integra el material Nylon 11 Powder en sus sofisticadas monturas de gafas de alta calidad y también utiliza las piezas de SLS como utillaje para la fabricación.
«Mi idea básica es que aspiramos a ser autosuficientes en nuestros procesos de fabricación, a poder influir en los procesos con mucha precisión y a seguir siendo siempre flexibles. Una impresora 3D que puedo llevar a mi propia oficina cumple exactamente esta visión».
Marcus Marienfeld
Producción en serie de monturas de gafas con la impresión 3D y la Fuse 1
A partir de este año, Marcus Marienfeld AG ha ido integrando cada vez más el nylon en la inusual elección de materiales -que van desde el carbono hasta el titanio, pasando por el cuerno de búfalo y la madera de antiguas barricas de roble- para sus gafas de lujo con la ayuda de su propia impresora 3D Fuse 1 SLS.
«Nuestras gafas son diferentes de las que existen», explica Marienfeld.
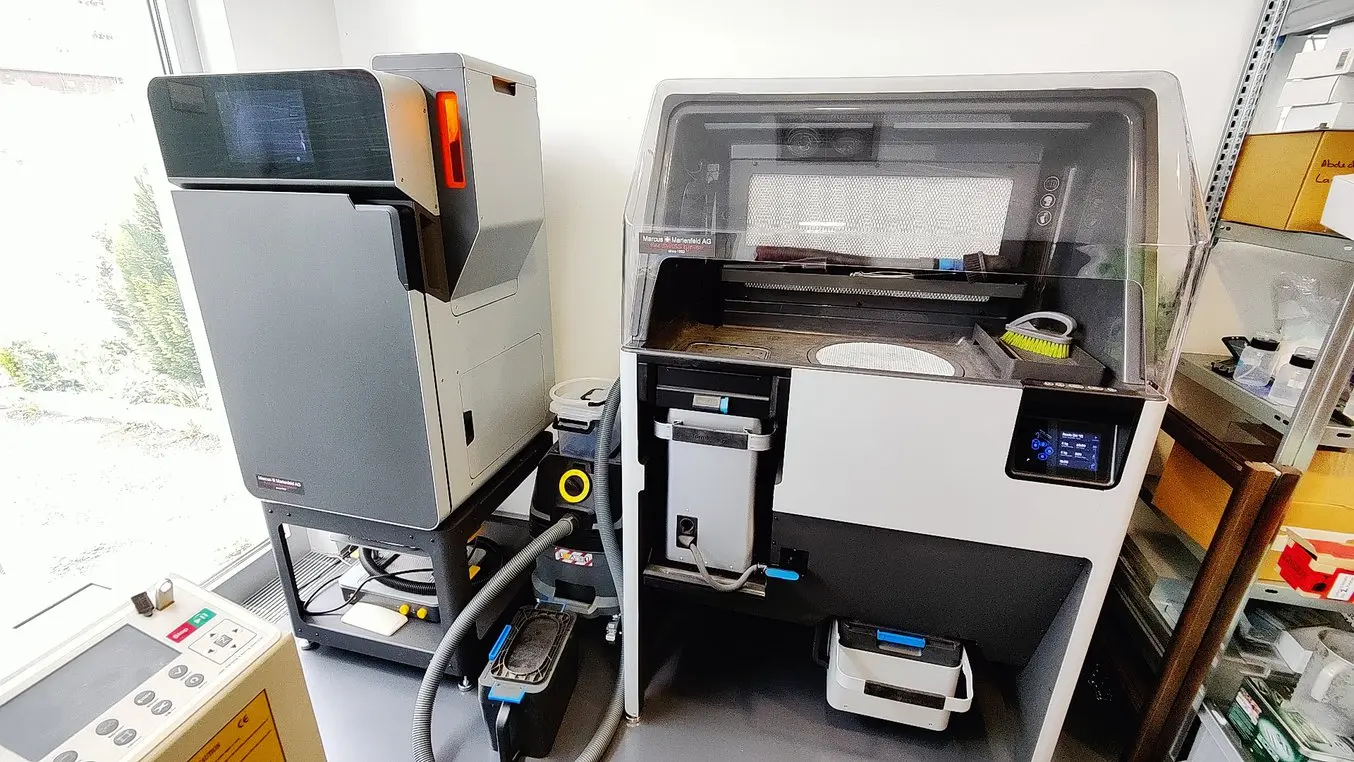
Con esta ambición, decidió incorporar el material Nylon 11 Powder de Formlabs a sus diseños de gafas. En primer lugar, se probaron en el estudio de Marienfeld muchos diseños diferentes, principalmente de frentes de montura impresos en la Fuse 1. También se utilizó recientemente la Fuse 1 por primera vez para fabricar una serie. En una sola impresión se pudo producir un total de 80 frentes de montura acabados en un periodo de aproximadamente 1,5 días.
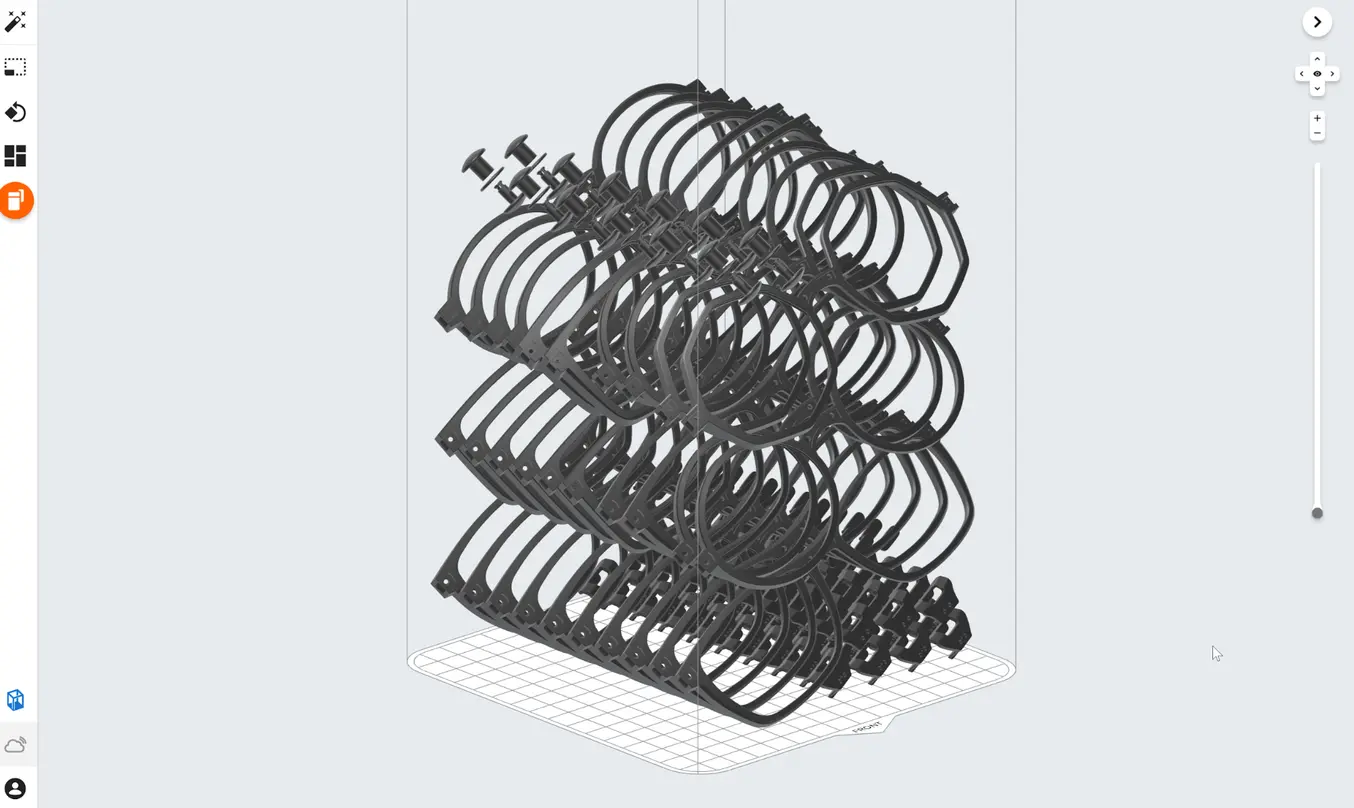
Gracias al gran volumen de construcción de la Fuse 1, se pudieron apilar y producir un total de 80 frentes de marco en una sola impresión sin estructuras de soporte.
Al ofrecer un alto nivel de detalle y no requerir estructuras de soporte, la tecnología de sinterización selectiva por láser de la Fuse 1 es adecuada para imprimir características de diseño delicadas que posteriormente se procesan con un ajuste preciso.
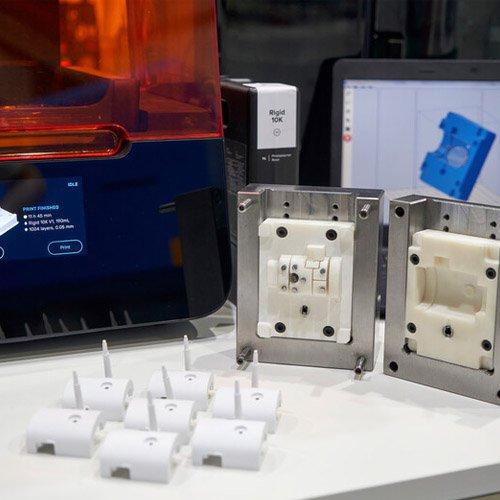
LIBRO BLANCO
Guía de la impresión 3D por sinterización láser selectiva (SLS)
En este libro blanco, cubriremos el proceso de sinterización selectiva por láser, los sistemas, los materiales, el flujo de trabajo para utilizar las impresoras SLS y sus diversas aplicaciones.
«Una de las grandes cosas de la impresión 3D SLS es que puede imprimir piezas anidadas sin estructuras de soporte».
Marcus Marienfeld
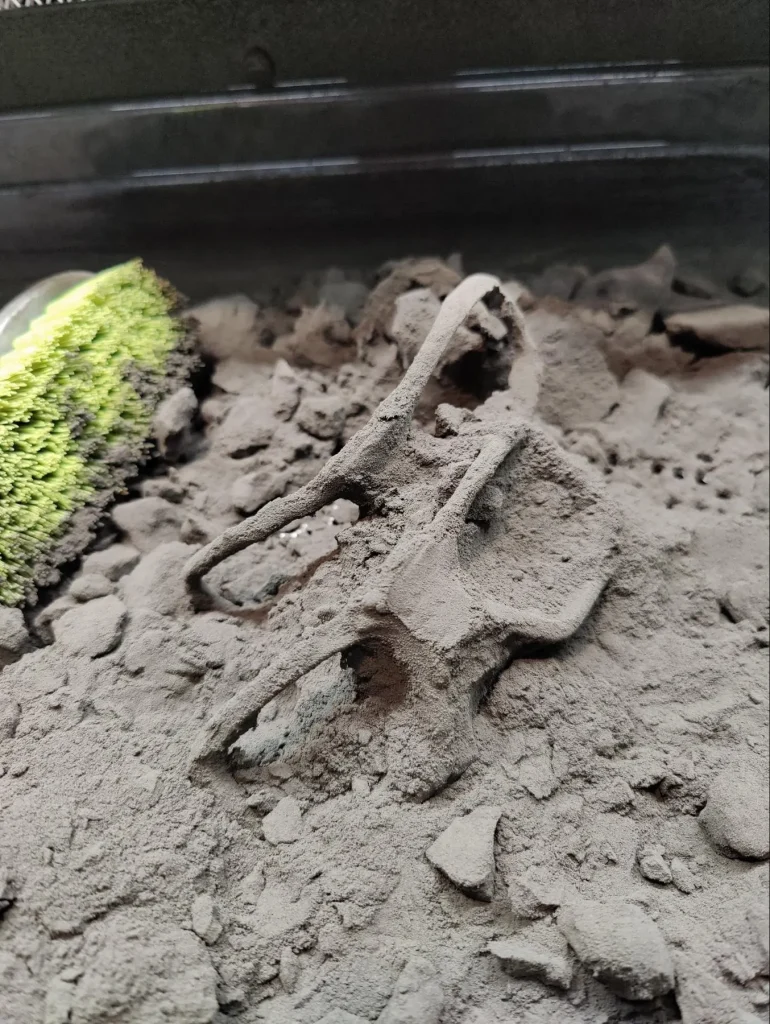
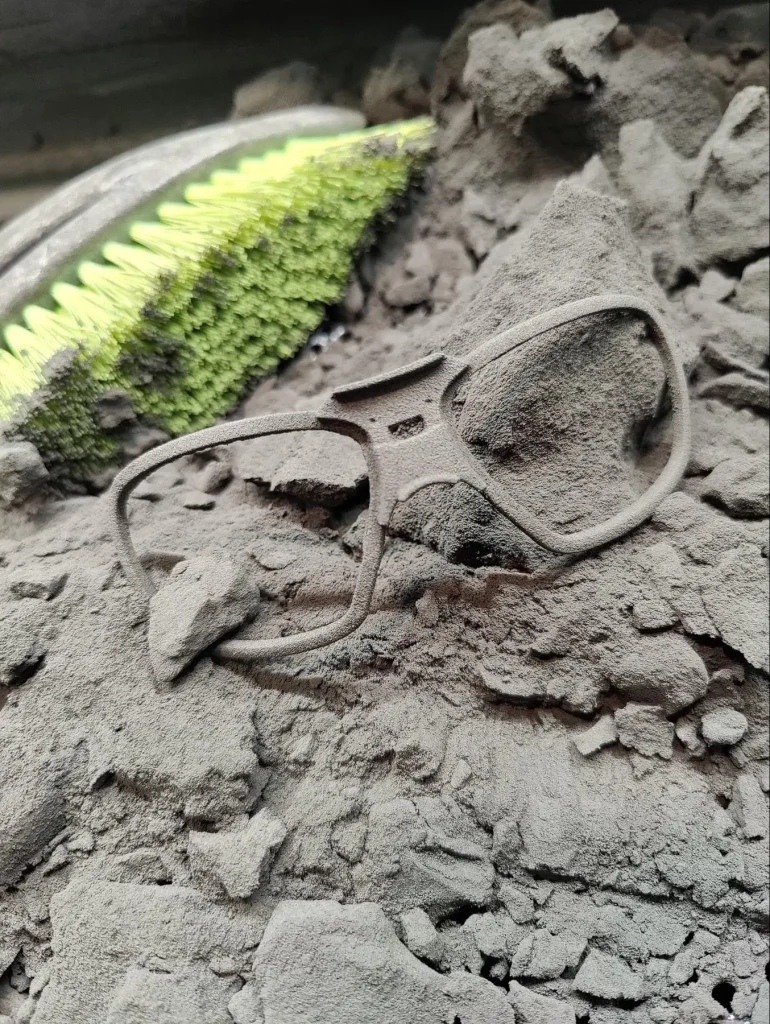
Monturas de gafas Nylon 11 Powder sometidas a un tratamiento posterior en el Fuse Sift.
Esta primera serie de gafas impresas en 3D con SLS se equipará con patillas de carbono de alta calidad y se venderá a socios de todo el mundo. Además, otros proyectos de gafas con elementos de nylon ya están en el banco de Marienfeld. Las gafas deportivas están diseñadas con ranuras de ventilación integradas, que se completarán con una impresión entrelazada.
«La Fuse 1 está siempre al 100% en términos de precisión. Eso es bastante impresionante».
Marcus Marienfeld
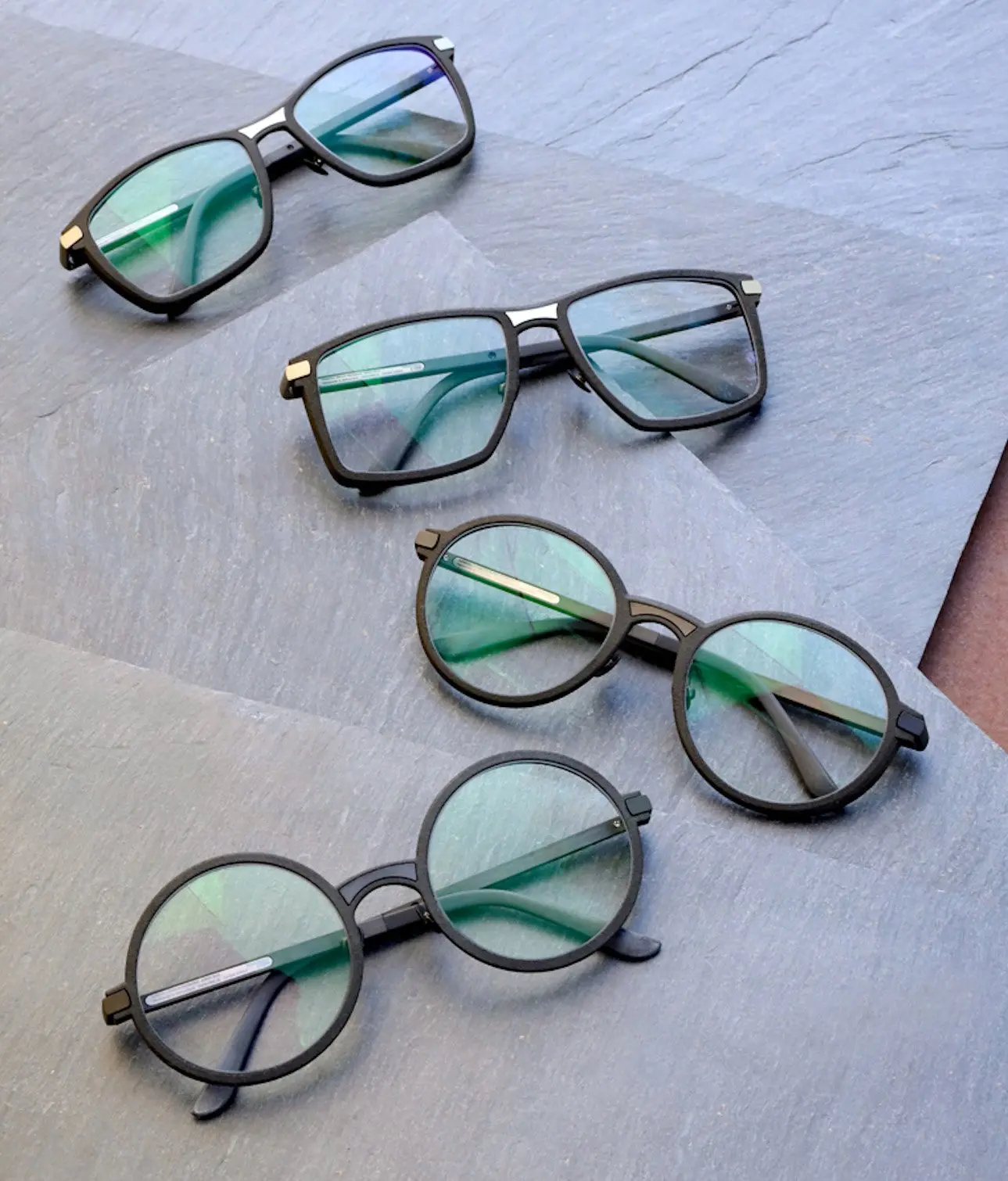
Gafas Marcus Marienfeld listas para usar en nylon 11 en polvo y carbono.
Las ventajas estéticas del material de larga duración de nylon
Mientras que propiedades mecánicas como la resistencia a la temperatura o la resistencia a la tracción final son importantes para muchos usuarios de Fuse 1, Marienfeld adopta una perspectiva completamente diferente.
A la hora de elegir el material, el diseñador optó por el Nylon 11 Powder principalmente por sus propiedades estéticas.
«Quiero destacar un poco el antracita oscuro del Nylon 11 Powder. Tiene un aspecto neutro y ahí se puede jugar con las combinaciones de materiales y, si se trata de joyas, se pueden combinar muy bien los elementos de color», dice Marienfeld.
Además, el acabado semibrillante, que sigue conservando cierto agarre tras los pasos de acabado, es valioso para vender las gafas Nylon 11 Powder y también para llevarlas.
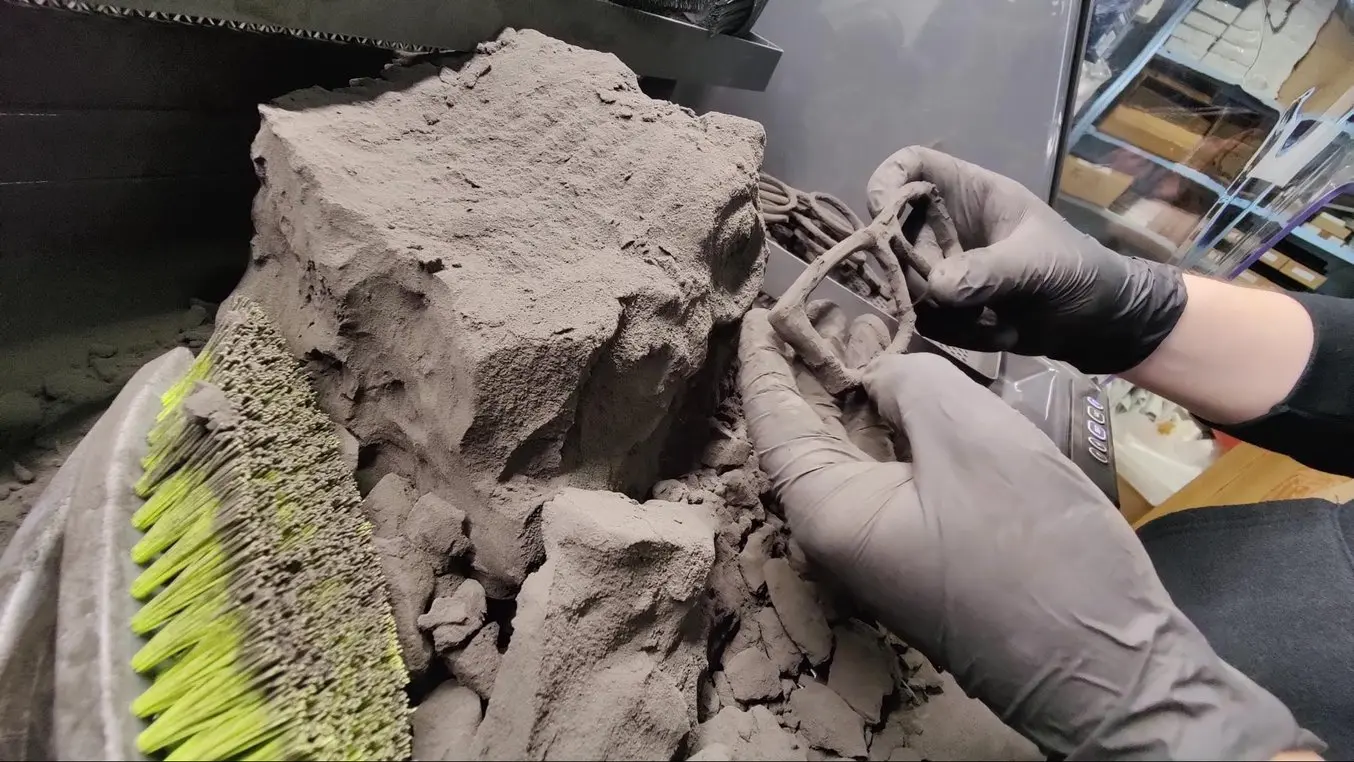
La impresión 3D convierten en realidad los deseos de los clientes individuales
Dado que Marcus Marienfeld AG lleva mucho tiempo utilizando también otras tecnologías de producción para sus gafas, se pueden establecer claras comparaciones entre el proceso de impresión 3D y los procesos tradicionales, como el mecanizado CNC.
Las gafas de carbono de Marienfeld se fresan en una máquina CNC de cinco ejes. En términos de detalle, hacen todo el trabajo, pero Marienfeld no puede hacer cambios individuales para proporcionar a cada cliente unas gafas que se ajusten perfectamente a su cara.
«Con la impresión 3D, puedo hacerlo inmediatamente. Si estás familiarizado con el diseño CAD, puedes hacer fácilmente ajustes en el modelo 3D, subirlo al software e imprimirlo directamente. En cambio, cuando se trata de fresar, siempre necesitaría un desarrollo de herramientas individual y costoso para sujetar los elementos en la máquina», explica Marienfeld.
Por ejemplo, pudo llevar a cabo la petición de un guía de montaña de un producto hecho a medida. Gracias al uso de la impresión 3D, en solo dos semanas pudimos entregar las gafas de sol de nylon con elementos laterales especiales contra los rayos del sol en la montaña.
«Con el carbono, que requiere métodos de fabricación convencionales, probablemente habría que contar con dos o tres meses para este tipo de producción», explica Marienfeld.
Herramientas impresas en 3D por SLS para moldear titanio
«El inconveniente del titanio es que es difícil de moldear, doblar o fresar. Pero se me ocurrió probarlo con una herramienta de prensado de Nylon 11 Powder impresa en 3D, y funciona perfectamente».
Marcus Marienfeld
«Fabricamos herramientas de prensado para doblar las monturas de cristal hasta darles la forma adecuada. Hay que crear una curvatura diferente de la montura según el modelo de las gafas. Antes lo hacíamos de manera muy laboriosa, con herramientas de acero, que suponen un alto coste por modelo», dice Marienfeld.
Este auxiliar de fabricación de Nylon 11 Powder, compuesto por una herramienta superior y otra inferior, se atornilla en una prensa de palanca en la fábrica y puede soportar una presión de aproximadamente 90 kilogramos. La excelente estabilidad dimensional del Polvo de Nylon 11 impide que aparezcan hendiduras en las herramientas en los lugares donde los bordes de titanio entran en contacto con la herramienta a tan alta presión.
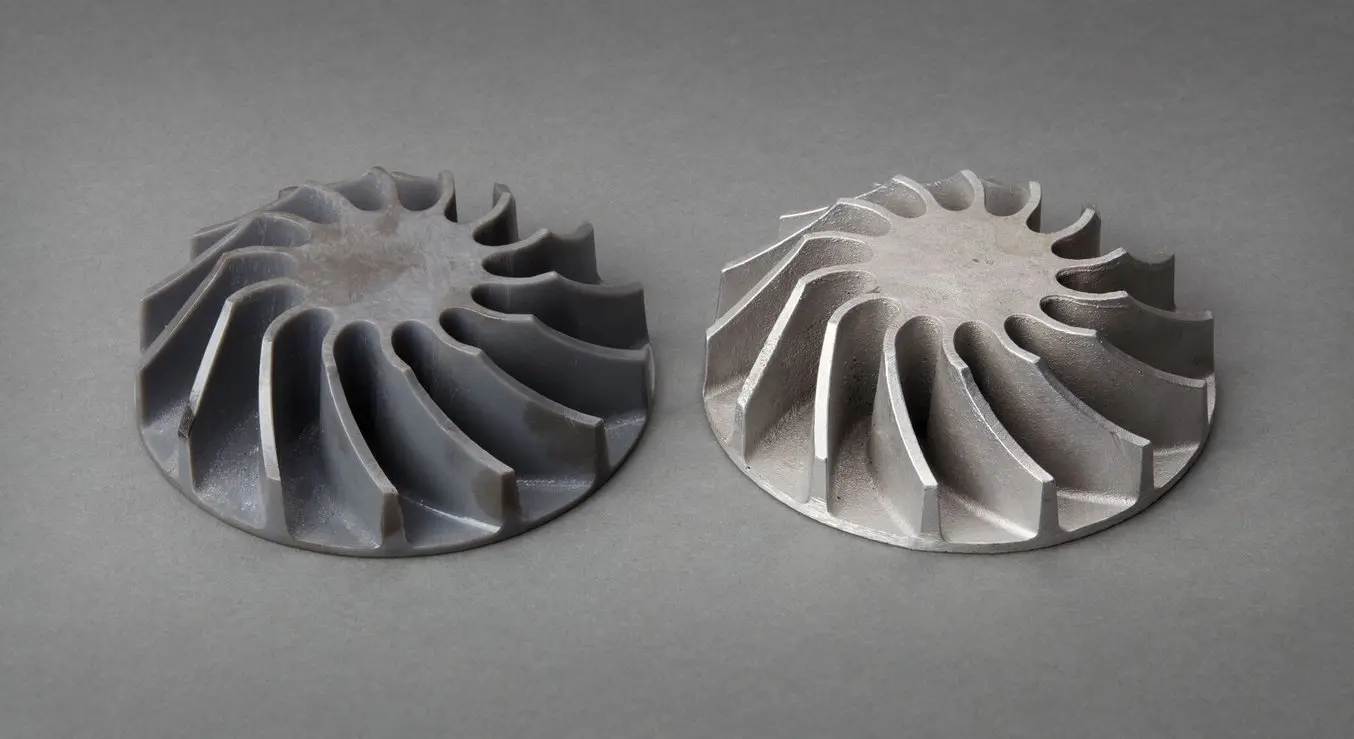
Modelo impreso con Grey Resin y fundición de aluminio acabada a partir de un molde de arena abierto.
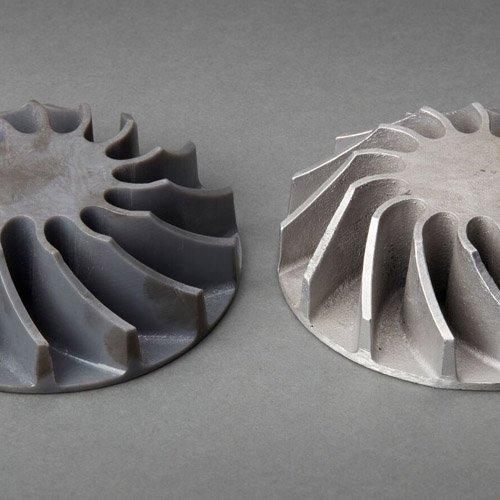
LIBRO BLANCO
Fabricación de piezas de metal mediante impresión 3D
Obtén guías de diseño para crear patrones impresos en 3D, ve paso a paso por el proceso de fundición directa a la cera perdida y explora las instrucciones de fundición indirecta a la cera perdida y moldeado en arena.
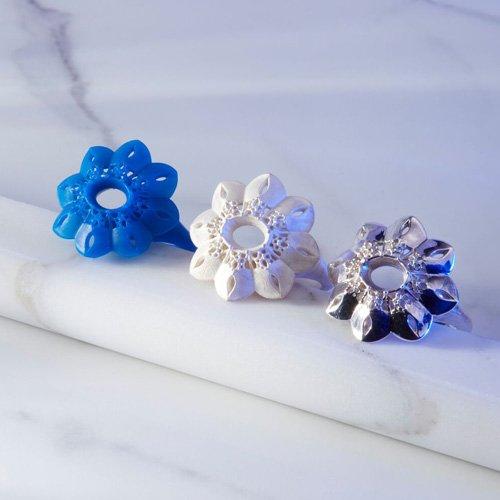
LIBRO BLANCO
Introducción a la fundición para patrones de joyería impresos en 3D
La forma de la que trabajan los joyeros está cambiando, y en la vanguardia de dicho cambio están las resinas fotopolimerizables. En esta guía, aprenderás a fundir piezas de joyería fina a partir de patrones impresos en 3D con impresoras de Formlabs.
Aparte de para los metales, la fundición también es un método popular para producir piezas de silicona y plástico para productos sanitarios, productos audio lógicos, aplicaciones aptas para la alimentación y más.
La empresa de productos sanitarios Cosm fabrica pesarios a medida de pacientes con trastornos del suelo pélvico. Sus empleados imprimen moldes en una impresora 3D SLA e inyectan silicona médica biocompatible en su interior para crear la pieza. El mecanizado rápido con la impresión 3D les permite crear piezas impresas sin los costes elevados del mecanizado tradicional.
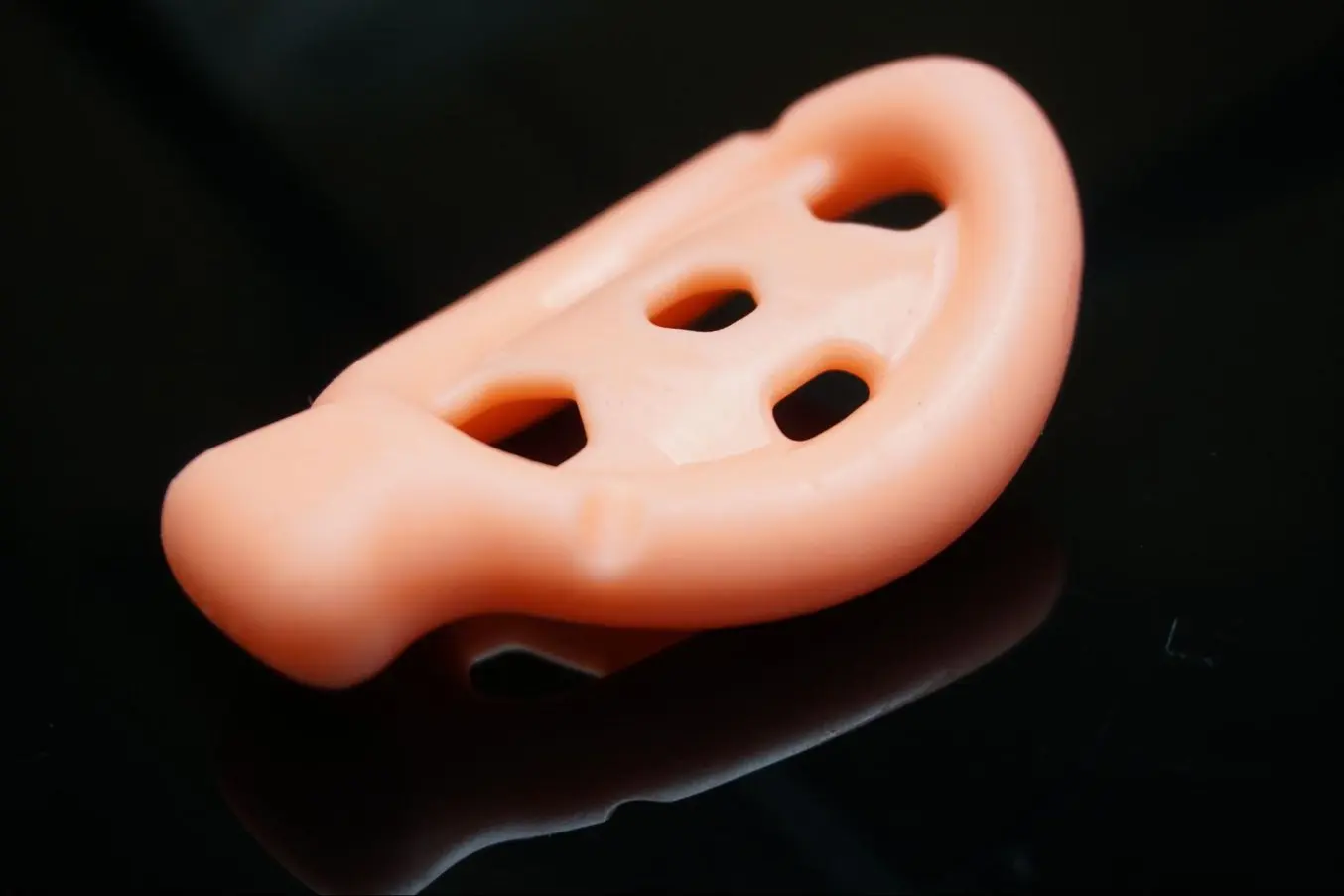
Pesarios adaptados a las pacientes producidos mediante fundición de silicona.
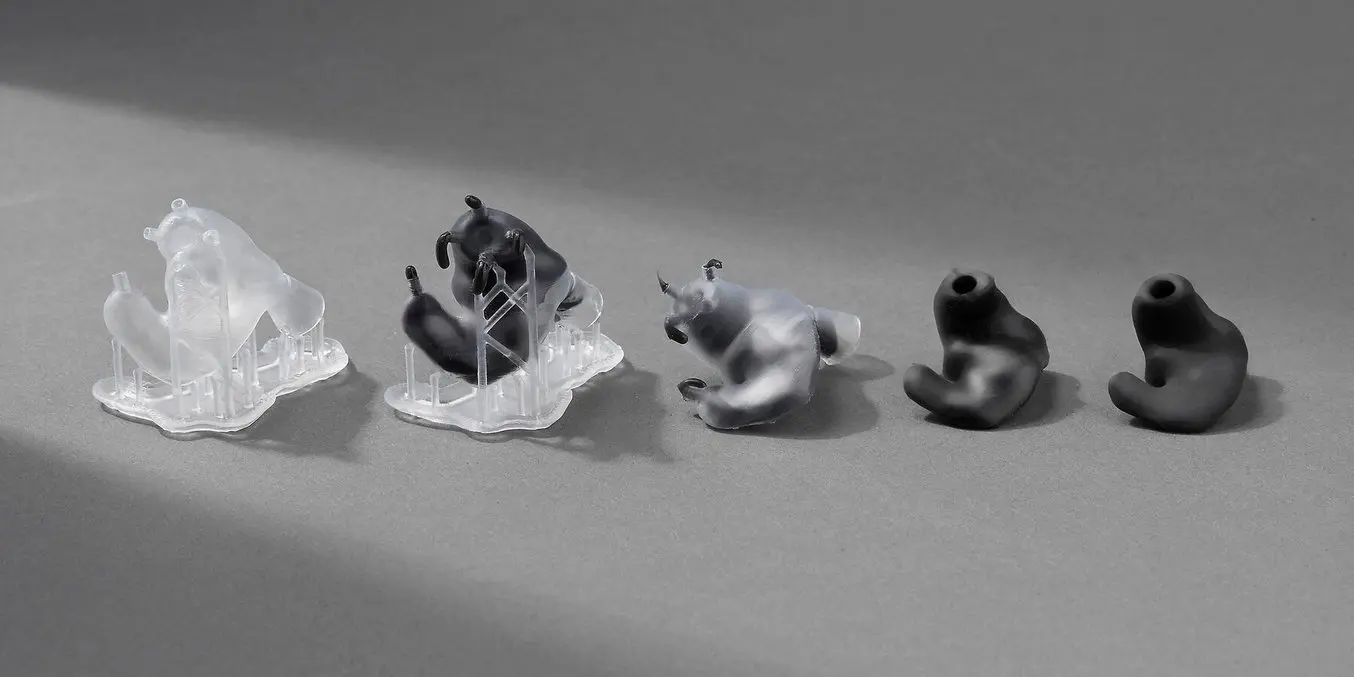
El proceso paso a paso de crear almohadillas a medida para el oído utilizando moldes auriculares de silicona.
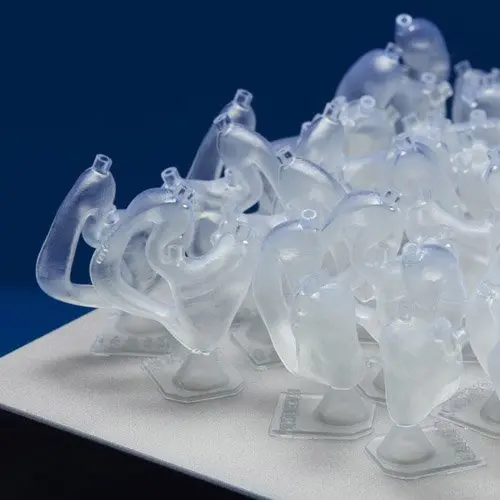
LIBRO BLANCO
Imprime en 3D moldes auriculares blandos a medida
Sigue la guía paso a paso para producir de forma asequible moldes auriculares de silicona personalizados usando una impresora 3D de Formlabs y la resina estándar Clear Resin de Formlabs.
Conformado de chapa
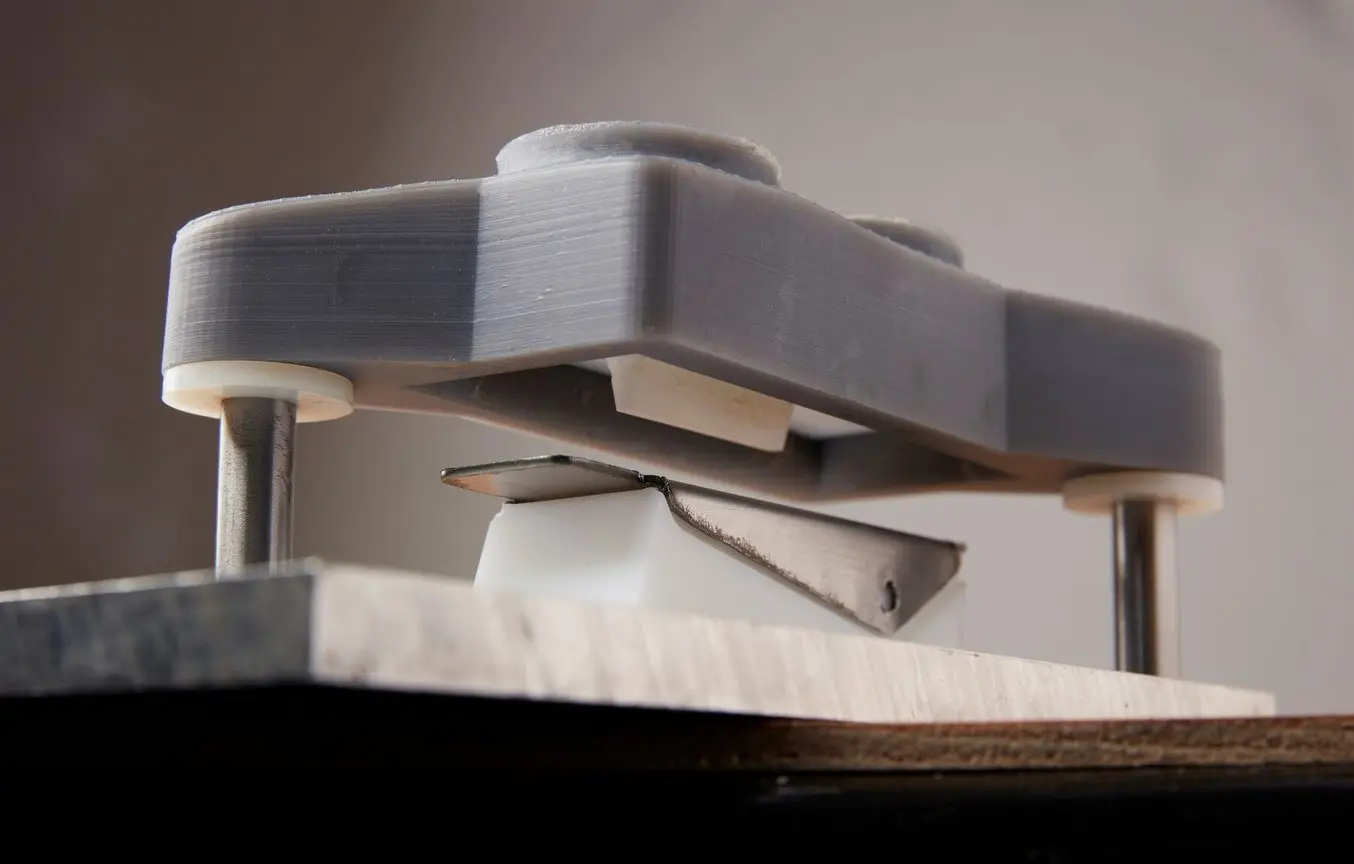
Diferentes iteraciones de troqueles superiores e inferiores fabricadas con la impresión 3D para conformar un repuesto de un protector de cuchilla.
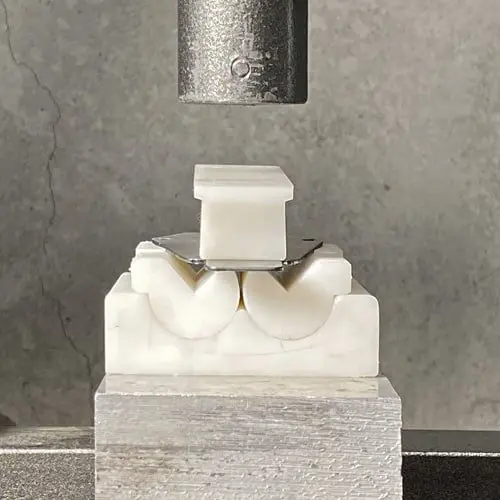
LIBRO BLANCO
Cómo hacer mecanizado rápido para el conformado de chapa con troqueles impresos en 3D
Esta investigación comprueba y demuestra la viabilidad de usar troqueles impresos en 3D mediante SLA para conformar piezas de chapa.
Conformado de chapa
Impresión 3D
La impresión 3D es el modo más rápido y asequible de producir mecanizado rápido para diversas aplicaciones. Como hemos visto en los ejemplos anteriores, el mecanizado rápido, tanto directo como indirecto, utiliza las capacidades de la impresión 3D de formas diferentes para desarrollar herramientas funcionales, como moldes, patrones y troqueles, para diversos procesos de fabricación tradicionales.
De entre los distintos procesos de impresión 3D, las impresoras 3D SLA son las que ofrecen las soluciones más versátiles para el mecanizado. Las piezas impresas en 3D mediante SLA son precisas, estancas, tienen un acabado liso de la superficie que es ideal para moldes y pueden reproducir detalles pequeños para moldes y patrones complejos.
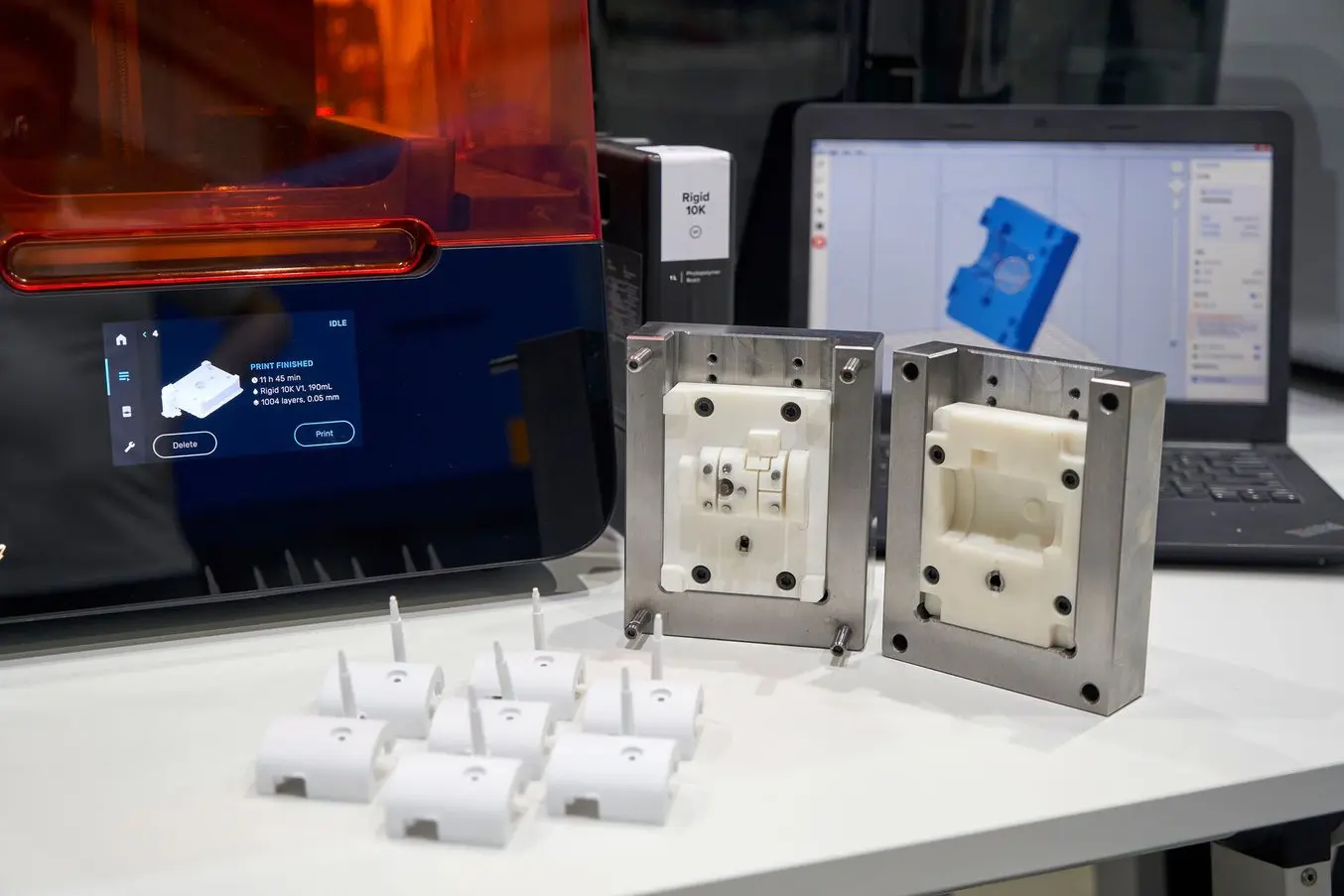
El utillaje rápido impreso en 3D es ideal para el moldeo por inyección de bajo volumen.
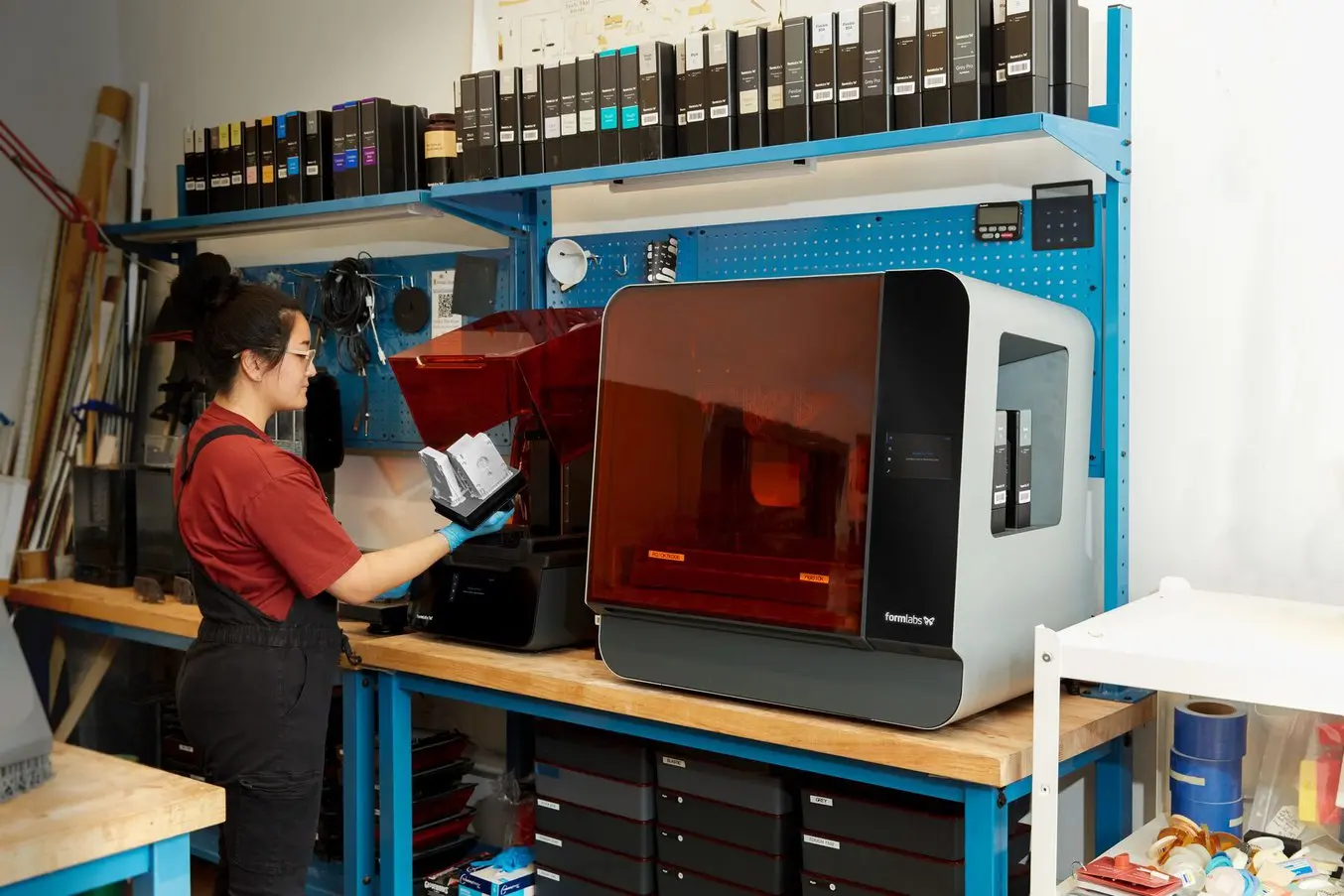
Las impresoras 3D SLA son fáciles de utilizar en tus propias instalaciones, con lo que el utillaje rápido se vuelve más fácil y más asequible.
Mecanizado
El mecanizado es uno de los métodos más comunes para fabricar mecanizado convencional y duro, pero también se puede aprovechar para crear mecanizado rápido. En vez de con metales resistentes como el acero o aleaciones de níquel, el rápido se suele mecanizar a partir de planchas para mecanizado, madera, plástico o aluminio.
En comparación con el mecanizado impreso en 3D, el mecanizado a partir de materiales blandos puede ser más eficiente para crear mecanizado de gran formato y formas sencillas, pero el trabajo manual y el dinero que exige crece de manera proporcional a la complejidad del diseño. El mecanizado de aluminio tiene mayor durabilidad y se suele usar para la producción de volumen bajo a medio, especialmente en el caso del moldeo por inyección.
Las herramientas de mecanizado son más caras, requieren un operario con formación específica y tienen un proceso de trabajo complejo para la producción in situ si se las compara con la impresión 3D, especialmente para piezas únicas como las iteraciones consecutivas de prototipos de mecanizado rápido. Por consiguiente, muchas empresas externalizan el mecanizado a proveedores de servicios, pero esto a menudo conlleva plazos de entrega que duran semanas y la rapidez del mecanizado rápido disminuye.
Compara los procesos de fabricación para el mecanizado rápido
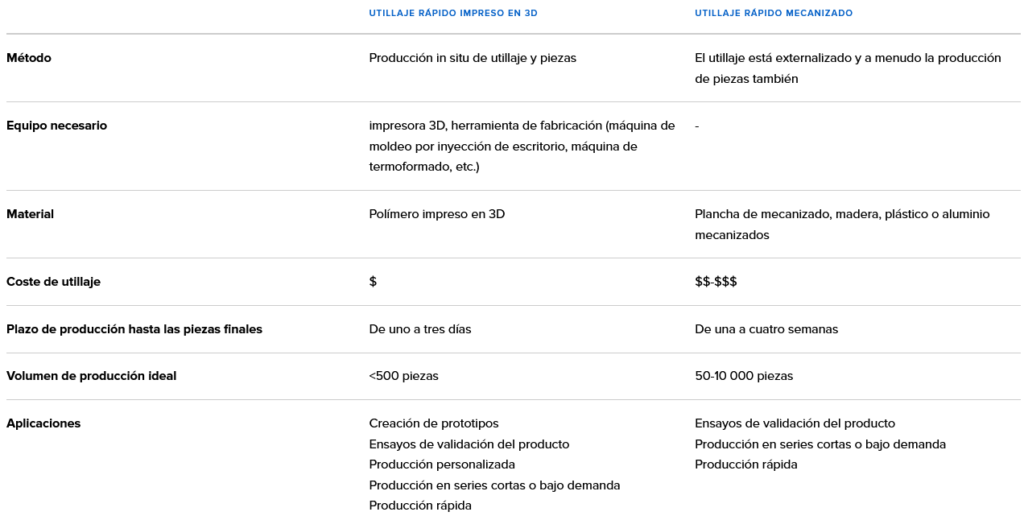
Cómo funciona el mecanizado rápido impreso en 3D
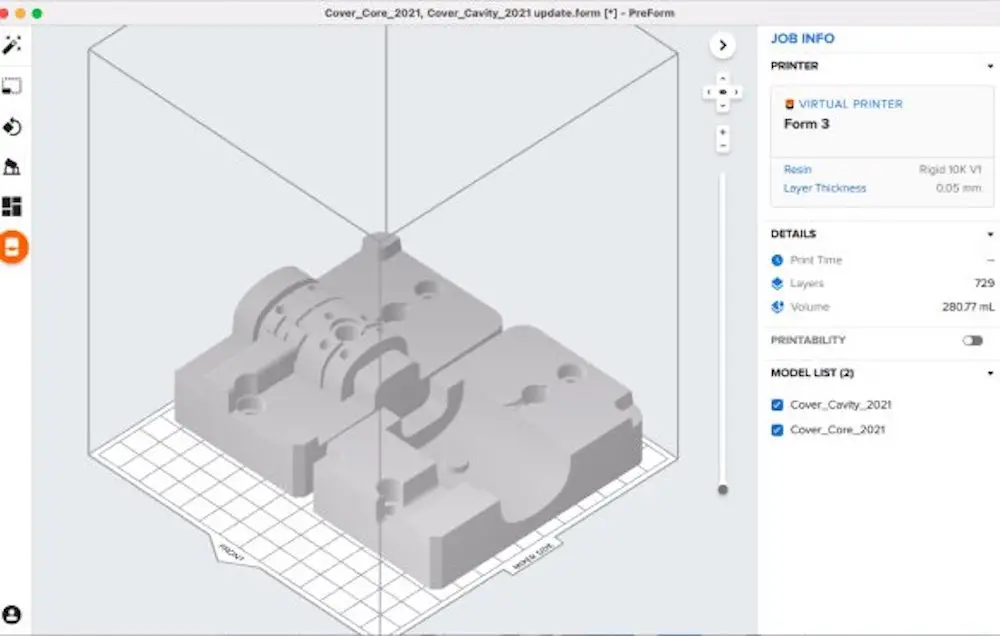
1. Diseño
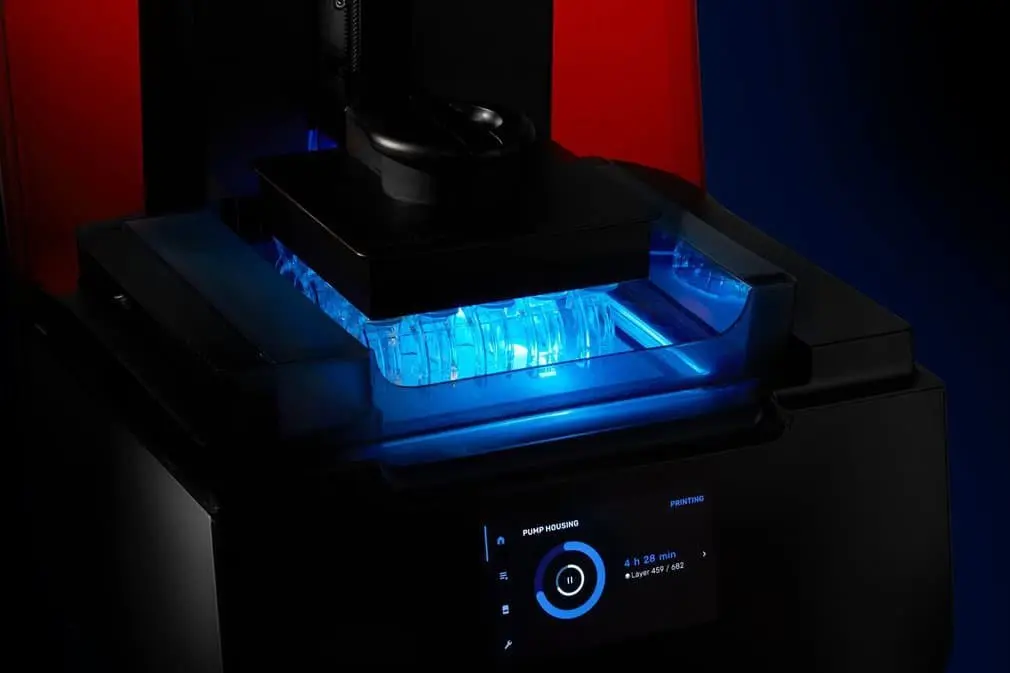
2. Impresión 3D
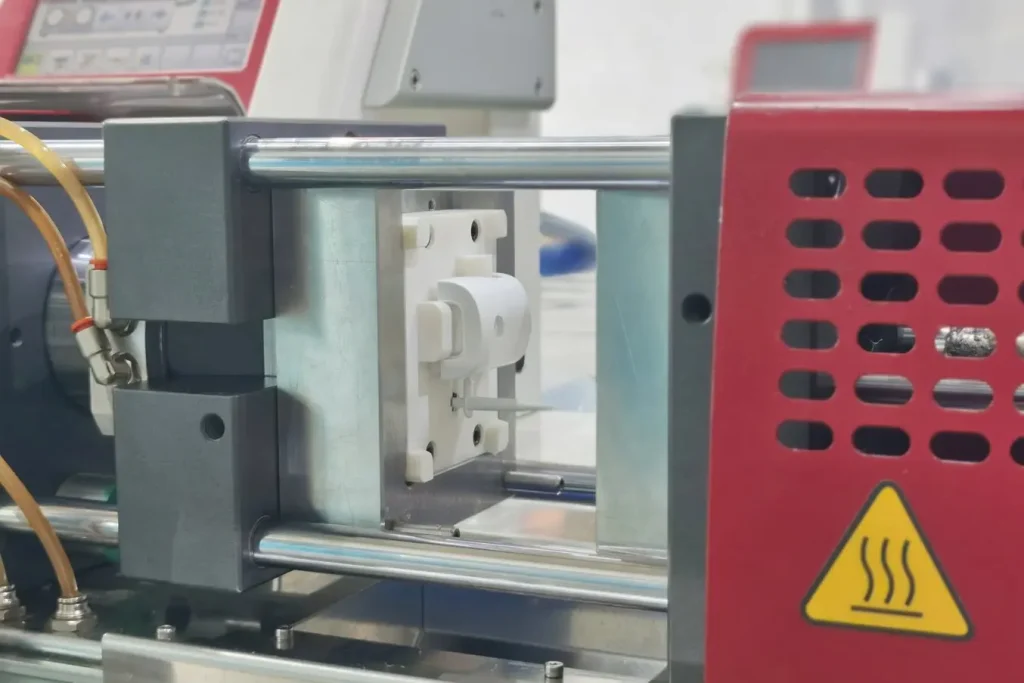
3. Fabricación
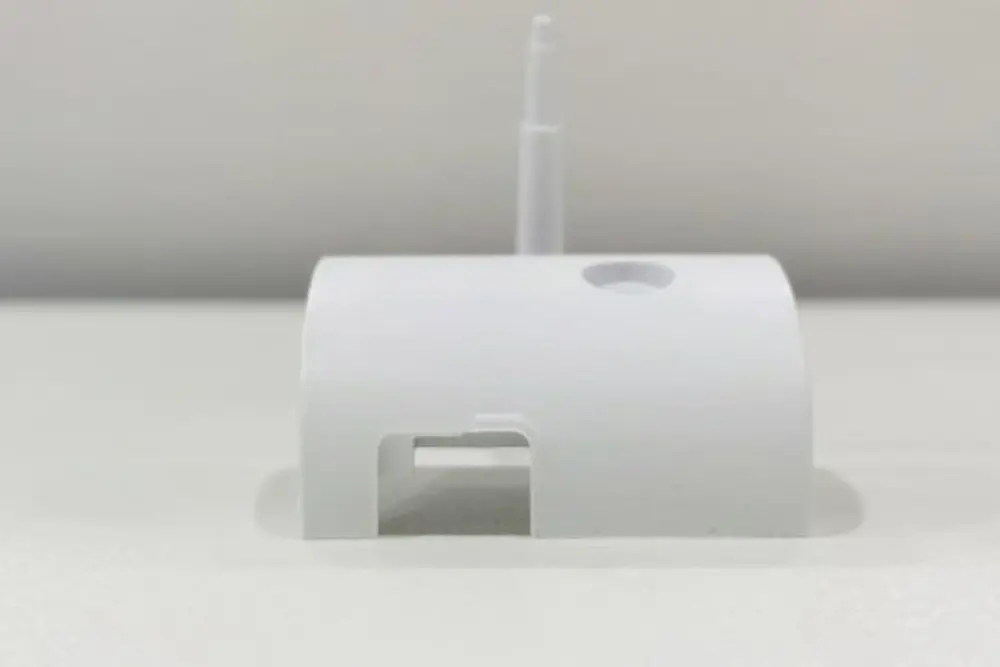
4. Posacabado
Empieza a crear mecanizado rápido
Combinar el mecanizado rápido impreso en 3D con procesos de fabricación tradicionales permite mejorar los procesos de producción mediante la mejora de su flexibilidad, agilidad, ampliabilidad y rentabilidad. Valida tu diseño y el material elegido antes de dar el salto a la producción en cadena y fabrica series personalizadas o limitadas de piezas de uso final.
Explora los diferentes procesos y descarga de nuestro sitio web libros blancos con detalles acerca de los procesos de trabajo, recomendaciones y casos de estudio reales. Si tienes alguna pregunta, ponte en contacto con un especialista en soluciones de Formlabs para empezar a trabajar.